Quality Assurance Process
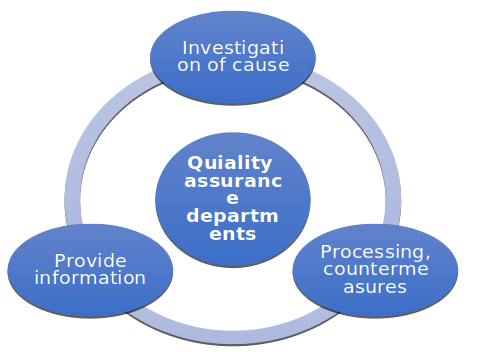
Customer Needs
Customer needs Various regulations, Examples of past defects
Defect information is fed back so that preventative and corrective measures can be implemented
Development
To improve the efficiency of development, members of production, purchasing, quality control, sales, service and distribution joint the design team in carrying out a design review.
Raw Material and parts Production
Emphasis is placed on audits of, and guidance for, suppliers. Results of inspection of goods purchased are fed back to suppliers, leading to quality improvement.
Production
Detailed checks are carried out to ensure that production plants have been met and that planned level of quality is attained.
Market information
Quality information on customers use of the product